Understanding LOLER in Regard to Health and Safety
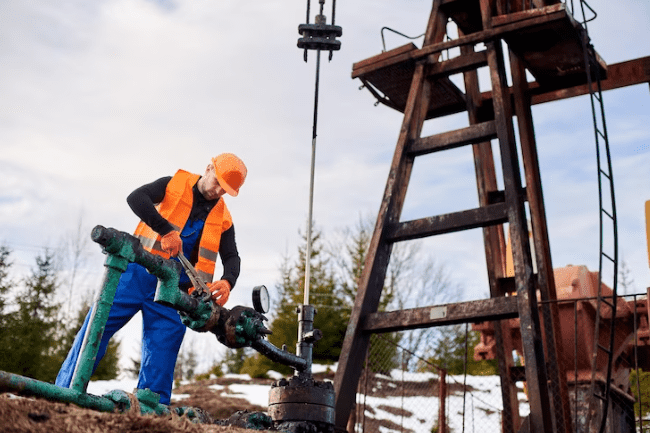
LOLER stands for Lifting Operations, and Lifting Equipment Regulations play a significant part in the health and safety of the workplace. Lifting operations are conducted daily in countless workplaces, ranging from healthcare facilities to warehouses and construction sites. But when carried out incorrectly, these lifting operations can create serious health concerns for the employees at the workplace. Therefore, properly using lifting equipment is crucial to prevent accidents and protect workers from harm. This is where the LOLER regulations govern the safe use of lifting equipment.
According to the Health and Safety Executive (HSE) in the United Kingdom, failures to comply with LOLER requirements have been identified as a contributing factor in numerous workplace accidents and incidents. These accidents can result in severe injuries, fatalities, property damage, and costly legal consequences for employers.
LOLER is a regulation that dictates law regarding all lifting operations conducted for work purposes. LOLER states specific responsibilities and duties for anyone who works with the lifting equipment at their workplace. The primary purpose of LOLER is to ensure that all the lifting equipment being used in the workplace is safe and does not pose any health risk to employees operating the equipment.
In this article, we will walk you through the definition of LOLER, its principles, what equipment it covers, and the duties placed on workers and employees.
What is LOLER
LOLER is a regulation that passes some laws related to health and safety concerns regarding all the lifting equipment used in the workplace to carry out lifting operations. This means that all the lifting operations in the workplace should be planned and carried out by a competent person. LOLER also further stipulates that lifting operations in the workplace must be properly supervised appropriately and those lifting operations to be conducted by trained employees who possess the skills to complete the tasks safely.
Under the LOLER Regulations, the lifting equipment being used in the workplace must be:
- Firm and strong enough to be used for the purpose intended
- Properly marked regarding its maximum load capacity
- Regularly inspected and maintained to ensure operations are carried out safely, minimizing downtime.
- Stored correctly in the prescribed manner or environment to ensure its longevity.
Three principle aims of LOLER
The three main aims of LOLER, as stated by the HSE, are:
- All the lifting operations in the workplace must be properly planned and managed.
- The condition of the lifting equipment must be good and safe for use.
- A competent person should thoroughly inspect the lifting equipment at suitable intervals.
What does the LOLER cover?
The regulation of LOLER applies to multiple workplaces that conduct lifting operations, such as:
- Construction areas
- Warehouses
- Factories
- Hotels and Restaurants
- Hospitals
- Offices
- Residential properties
- Care houses
Some examples of lifting equipment covered by LOLER include:
- Cranes
- Lifting trucks
- Telescopic handlers or booms
- Pallet trucks
- Pulley systems
- Vehicle hoists
- Mobile elevated work platforms (MEWPS)
- Rope systems
- Patient hoists
Key provisions of LOLER
Thorough examination
Under LOLER, lifting equipment must undergo a thorough examination by a competent person at specified intervals. This examination is distinct from routine maintenance and ensures ongoing safety. By subjecting the equipment to regular inspections, any potential faults or issues can be identified and addressed promptly, reducing the risk of accidents or failures during operation.
Inspection and Maintenance
Regular inspections and proper maintenance are vital to safely operating lifting equipment. These inspections help identify any wear and tear, damage, or malfunction that may compromise the equipment’s integrity. The equipment can be kept in optimal condition by promptly addressing these issues through maintenance and repair, minimizing the risk of accidents. LOLER emphasizes that competent individuals with the necessary expertise and knowledge should carry out inspections.
Safe working load
LOLER mandates that lifting equipment be marked with its safe working load (SWL). The SWL indicates the maximum load the equipment has been designed and rated to lift safely. Operators must adhere to the SWL specifications to prevent overloading, which can lead to equipment failure or collapse. By following the SWL guidelines, operators can ensure the safe and efficient use of lifting equipment.
Training
Proper training and competence are essential for individuals operating lifting equipment. LOLER recognizes the significance of providing adequate training and instruction on safe practices, risk awareness, and emergency procedures. Working with lifting equipment can be very hazardous and risky for the workers, and therefore it is important that these workers are properly trained on courses like LOLER training or Lifting equipment training, as well as other training that would educate these workers on how they could ensure their safety while operating this equipment and assuring their compliance with the regulation.
Planning and Organization
LOLER places importance on lifting operations’ planning, organization, and supervision. Employers must conduct thorough risk assessments, considering factors such as load weight, environmental conditions, and the suitability of the lifting equipment. Implementing appropriate control measures, such as providing safety barriers, ensuring proper communication, and establishing emergency response procedures, enhances the overall safety of lifting operations.
Siting and Positioning
The proper siting and positioning of lifting equipment are essential to prevent accidents during operations. LOLER emphasizes the need to correctly position and stabilize the equipment, ensuring it is securely anchored or supported. Following these guidelines can significantly reduce the risk of equipment instability or collapse.
What are your responsibilities under LOLER regulations?
LOLER dictates many legal duties and obligations on employers and employees in regard to the use of lifting equipment. These responsibilities include:
Suitability – Lifting equipment should be appropriate for the task at hand. It must be built and modified to suit the task at hand. Employers must guarantee that the relevant equipment is available.
Strength – Lifting equipment must be sufficiently sturdy to withstand any forces that may be applied to it, such as the influence of wind on a crane. Lifting equipment must be stable enough to prevent it from tipping over. For example, so that it is not readily blown over in an outdoor setting.
Safe installation – Lifting equipment must be properly positioned and installed to avoid damage. This must be done to reduce the possibility of loads falling on or striking somebody.
Markings – Lifting equipment must be visibly marked, with the appropriate warnings and labels, in addition to identifying information such as the safe working load.
Appropriate use – Lifting operations must be planned, overseen, and completed safely.
Safe lifting of people – There are extra conditions that must be met when lifting equipment is used to raise persons. The equipment must be labeled as safe and fit for purpose.
Precautions – All precautions must be made just in case the plan goes in the wrong direction.
Inspection – Lifting equipment, including attachments, must be subjected to a variety of inspections, including pre-use checks performed by the user each time lifting equipment is used and complete exams performed at regular intervals by a properly competent person. In addition to rigorous exams, more sophisticated lifting equipment may require regular inspections.
Training and instruction – Employees must be properly trained to ensure their well-being while operating lifting equipment. Such as those workers dealing with work at height should be properly trained to conduct such dangerous work and also on the use of PPE to ensure safety. These training programs can include working at height training, risk assessment training, harness and lanyard training, PPE training, etc.
Conclusion
LOLER is vital in safeguarding workers and promoting safety in lifting operations. By establishing regulations for thorough examinations, inspections, maintenance, and training, LOLER ensures that lifting equipment is used correctly and safely.
Harness and lanyard training, in line with LOLER requirements, further enhances worker safety by addressing fall hazards. By adhering to LOLER and providing comprehensive training, employers can create a safer working environment, prevent accidents, and protect the well-being of their workforce.
Visit Here cbdcannabis360.com for more blogs